Remote Control System for propulsion plants
RCP2000
The RCP2000 is a customizable remote control system for main and auxiliary propulsion plants. This fully automated control system has been approved by all major ship classification societies and can be adapted to different thruster configurations. The system was developed as a product replacement for the very successful AFA1 and AFA5011 remote control systems, of which more than 500 units have been delivered.
Application areas
Since 2002, our company has delivered more than 250 RCP2000 control systems. The system is constantly improved and adapted to new requirements.
- Main Propulsion Remote Control for Controlled Pitch Propeller
- Transverse Thrusters with motor starter and electrical drive motor
- Azimuth thruster with CP or FP Propeller
- Water-Jet with frequency controlled prime mover
Flexibility
The RCP2000 remote control system is a modular system that was designed to meet the needs of our customers. The system supports various control stands in the wheelhouse and additional control stands in the engine and thruster room. Interfaces for DP, joystick control and autopilot are integrated. The top panel design can be custom-made. The control system provides a wide range of features such as engine load control, drive programs, combinator mode and constant speed mode, clutch control, alarms and more.
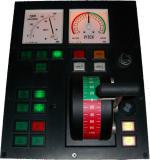

Control features
-
Drive programs: free programmable programs for free running, manoeuvre, fire fighting and for DP/JS operation
-
Steering and drive modes: free programmable propeller curves for constant speed mode and combinator mode
-
Clutch control: integrated clutch control system with adjustable clutch window clutch monitoring
-
Load controller with load protection, chief limitation and load distribution system
-
Colored touch panel diagnostic and service panel with online alarm history
-
Bus-line communication for reduced cabling effort
-
Condition Monitoring with integrated process recorder and real-time process analysis for early wear detection of mechanical parts
External interfaces (VDR, DP, Joystick, IBS)
The control system can be also easily integrated into an IBS (integrated bridge system) via an Ethernet network connection. If the IBS system provides remote access to the ship's network, remote diagnostics are also possible from other locations. Other external systems such as VDR, Conning, and the Ship Alarming System can be linked via a hardwired connection or a serial NMEA communication.
Web-terminal for diagnostic and configuration
The control system is equipped with a remote diagnostic system which can be accessed using a simple local touch screen or a web browser from the office, and provides the operator with a clear overview of the system status. A complex monitoring and error-handling system ensures that the system remains in a defined state. Every alarm is indicated acoustically and visually by button indicators or a buzzer. The system divides the faults according to their degree of severity. The system additionally includes a complete alarm system. Each alarm is stored with a plain text timestamp. Access to the alarm system is possible through the touch panel operator screen located in the engine control room.
The internal monitoring system is capable of detecting external faults by analyzing the process parameters. For example, a hydraulic failure is detected by comparing the response of the hydraulic system with the expected result from the simulation.
Product replacement and retrofittings
Due to its flexibility, the system is not only designed for use in new vessels, but can be also used as a replacement for old control systems. The system can guarantee the same functionality as the old system while providing the features of a modern control system. Furthermore, SER provides customer support that draws on more than 60 years of experience in the field of marine systems.
Bridge Control Unit
The RCP2000 can be equipped with customized command stations. In addition to the main control panels in the wheelhouse, further control stations are possible in other locations (e.g. the moon pool). The bridge control unit also connects all external interfaces such as DP, Joystick, Conning or VDR.
Engine Control Room Control Panel
The ECR panel provides additional functions such as chief limitation, RPM fine adjustment for shaft generator mode and the remote panel for the hydraulic pump starter. Furthermore, the integrated diagnostic touch panel indicates each alarm with a specific alarm text message.
Central Unit
The Central Unit is the CPU of the remote control system. This unit is responsible for pitch and rpm regulation.
Local Unit
The Emergency Control Stand is located near the hydraulic aggregate. It provides the option of driving the pitch manually with the help of the push-buttons.